How are prefab houses made?
Prefabricated homes have risen hugely in popularity among developers, architects, investors, landowners and, with the announcement of Westpac's new prefab home mortgage, now first home buyers. There are many benefits that come with choosing a prefab home, after all, they are constructed off-site in a warehouse which limits the effects of the weather, they are quick to build, and they are also very affordable.
But the idea of a house being built in a factory seems an alien concept. We're so used to seeing a house take shape slowly, fully exposed to the elements, that the idea of one being delivered to site like a MightyApe parcel just doesn't compute!
One of the strangest parts of building a house in a factory is that it moves along a production line in a similar fashion to how your car did when it was built, with different activities undertaken at each stage. To help you visualise how a house is built we've opened the doors on our factory in Timaru to explain the stages each house goes through before hitting the road and heading to its forever home.
Journey with us and follow a home as it goes from bare frame to finished abode in as little as 18 weeks.
Stage 1: Floor construction, and frames standing
Steel subframe
Every home we build begins as a steel subframe. This subframe will be cemented into the foundation or piles when it arrives to site. It also helps provide the rigidity required to ensure the home doesn't move when transported.
Unlike a transportable home, our homes will be forever fixed in place when they arrive on-site. The subframe creates the connection point between the home and the ground.
Studies have shown that, surprisingly, the steel subframe can actually add an additional layer of protection during an earthquake as it provides additional rigidity, strength, and reduces the lateral forces applied to the home during an earthquake. This steel frame dictates the total floor plan of the home so there's no chance of extensions after this stage!
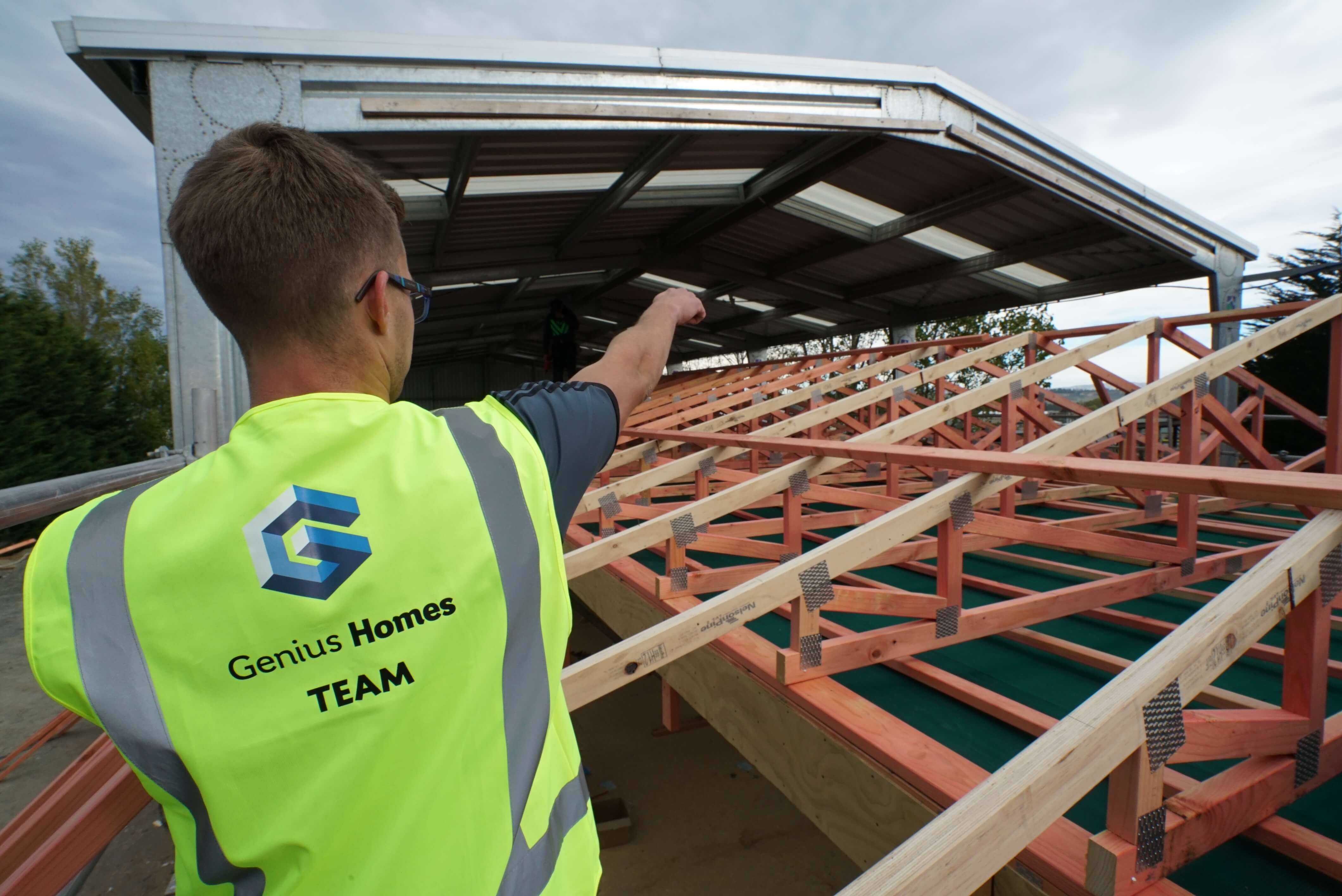
Wooden framing
Next comes the wooden frame for the home. During the planning phase, the owner's Genius Homes planner would have worked out the floor plan and layout. Even though each home comes with a pre-designed plan it's possible for owners to change walls around and even lengthen their home during the planning stage should they wish. All of that is locked in before the framing is built.
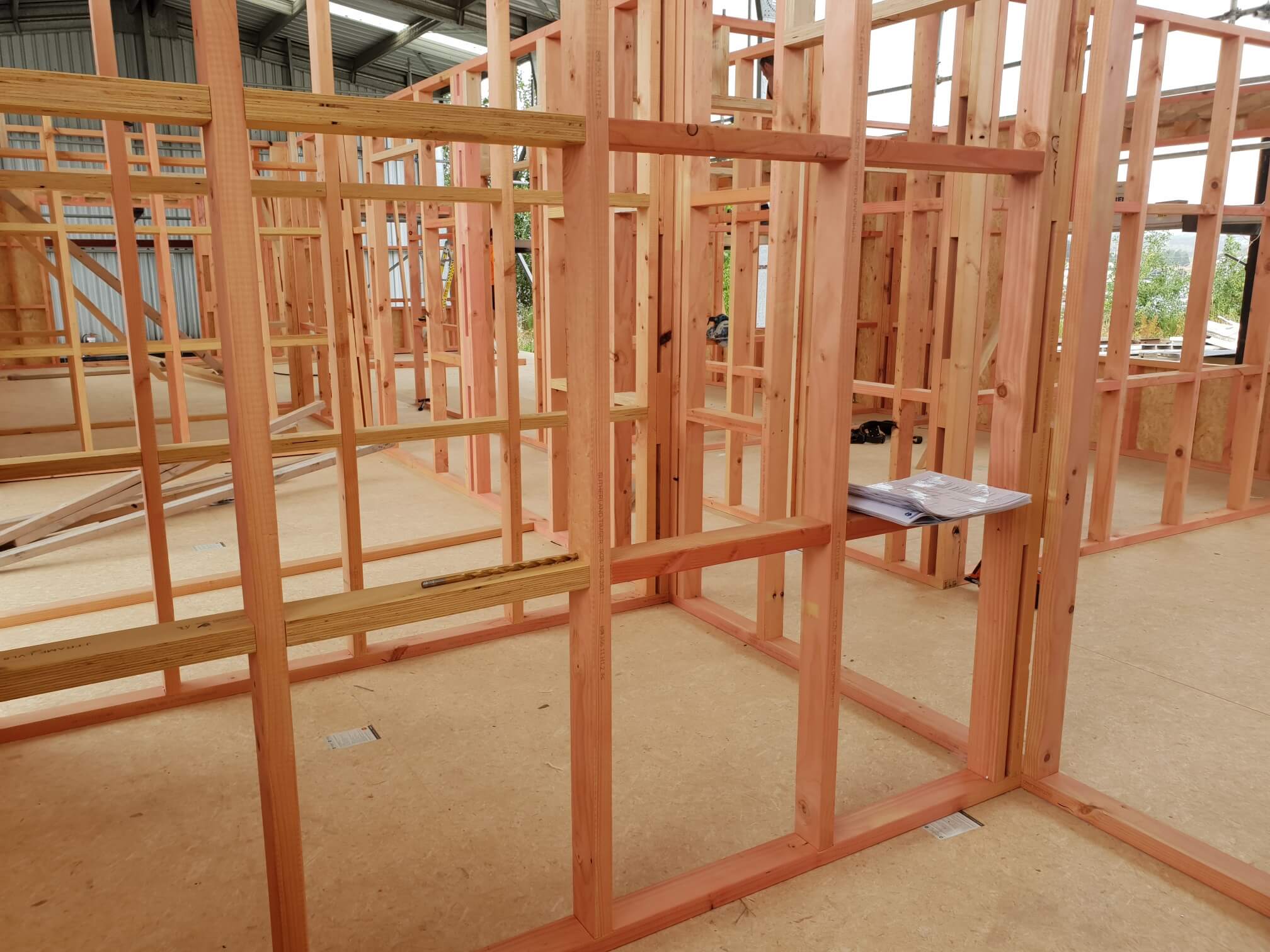
Stage 2: Building closed in and internal lined
The next stage is closing the home in and putting on the roof. This is the beginning of making the house weather tight and, depending on the weather as well as capacity, we can elect to conduct this stage inside or out.
You can see in this first image that the frame within the building is still bare but we now have a brand new roof on and the external walls are beginning to go on. This home will soon receive its windows and doors and will then be weathertight.
The above home is enjoying the great outdoors. When the weather is good we may choose to use the external production line to allow more homes to be built at once - this is often the case during the summer months.
If the weather's a bit grotty we may build the home completely indoors. You can see here that we have a home that is weathertight now that it has the windows and doors on.
At this stage we will begin work on the interior. This is where our homes become a hive of activity as different teams work like clockwork to complete our homes as quickly as possible. Because we have a team of tradies on staff we don't need to worry that another job will take priority over our homes. When we do use subcontractors the timeframes for our homes are very rigid so we can tell them exactly when they'll be needed, which allows them to project manage effectively.
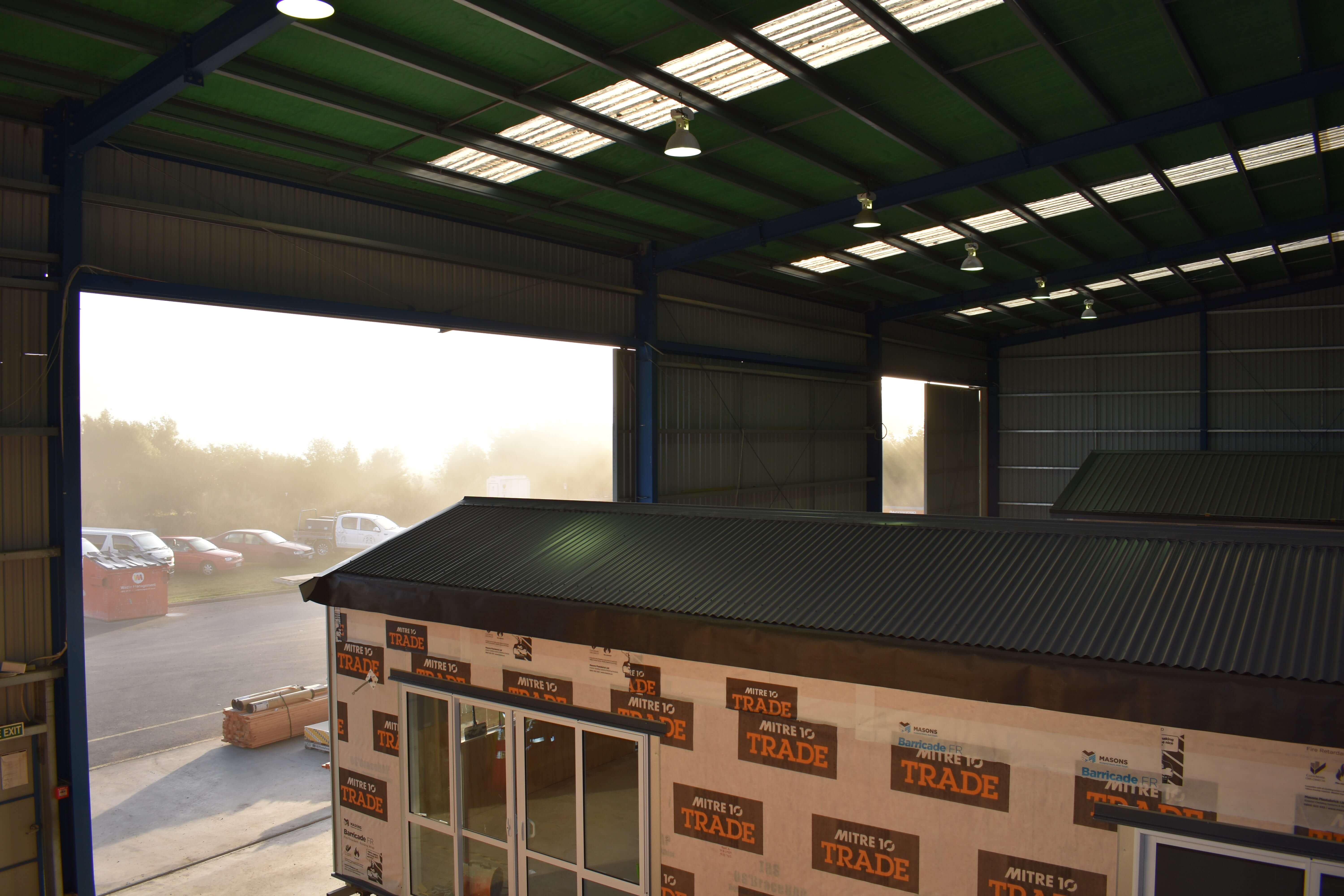
Sitting pretty in our warehouse
Stage 3: Cladding installed, internal stopping and painting completed
This is where the house really starts to come together and where the pace of activity picks up! While the external cladding is going on the internal teams begin to put up the GIB, and the architrave, coving and skirting is added.
In the image to the above you can see the edge of a home about to move to the cladding stage. We offer a wide range of cladding options including board and batten, weatherboard and wood finishes like cedar.
Much of the wiring would have been installed as the GIB and insulation was going in, making it easy to pull through once at the required stage.
One of the fun parts of planning your home is deciding where things like plug sockets will go, and how many you may need to charge all of your devices! For example, it's a good idea to think about where a TV may end up as these often require a few more sockets to handle the TV itself, plus any extras for things such as SKY boxes and games consoles.
Considering heating is also something your home consultant will raise early in the planning process. Almost every Genius Homes house comes with a heat pump as standard and you may want to put some extra thought as to where that may go. If you want gas heating then this can be installed very easily.
Because our homes are so well insulated it's often the case that a single heat pump or wood burner will heat the whole house easily but if you want something like a home ventilation system added then this can also be discussed during one of your early consultations.
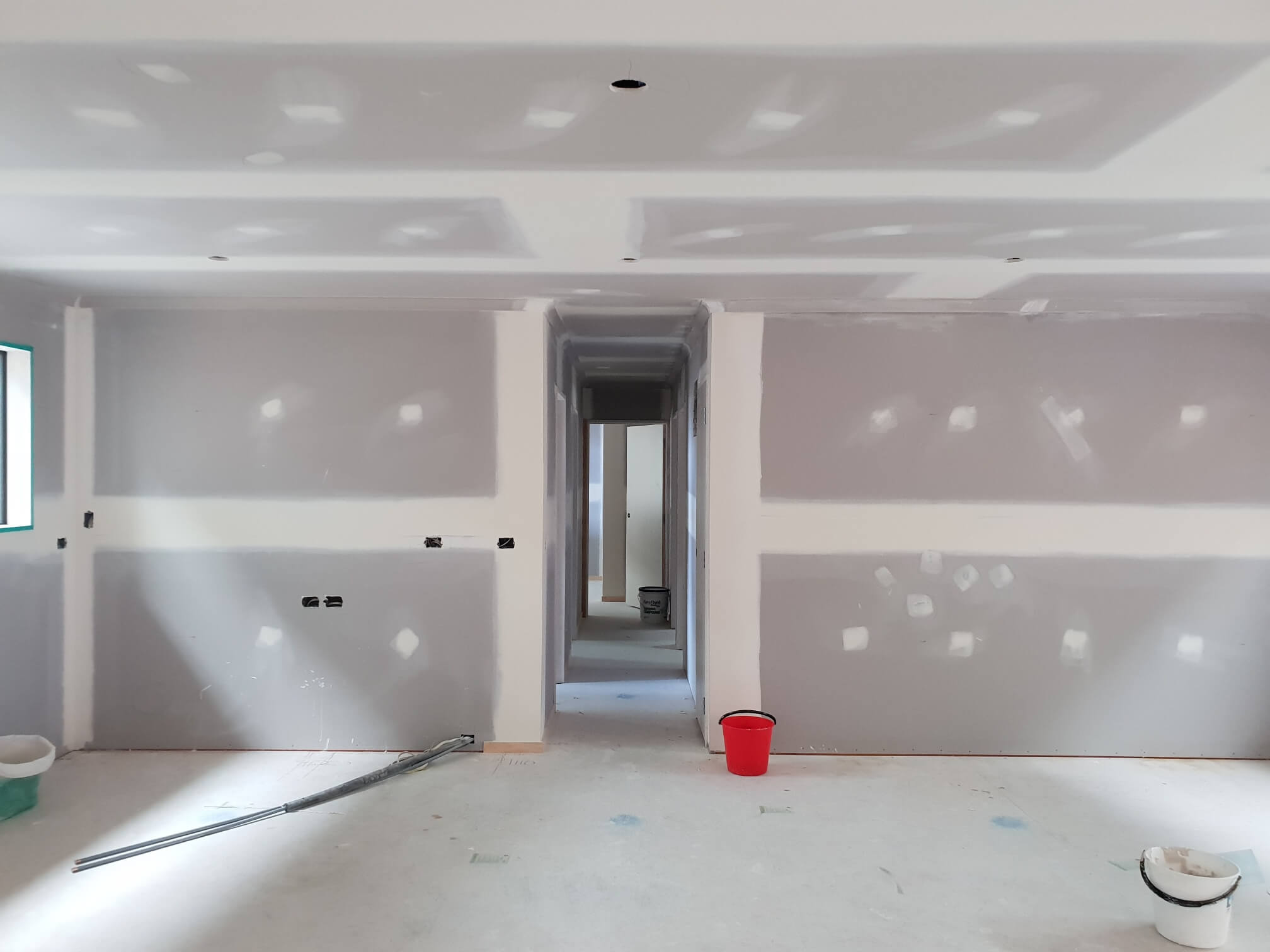
Walls lined, internal stopping completed
Stage 4: Internal fit-out and fit off.

If you want to see this process for yourself because you're considering a prefab home and want to know more before you commit, then you'll be pleased to hear that we offer free factory tours of our Timaru facility.
Not only is this a great way to better understand the prefab home process but it also serves as a great way to be inspired for your own home. Whereas we can't guarantee that your dream Genius Home design will be in production during your visit, we can show you similar homes and discuss what you're looking for in your dream home.
If you choose to build with us then we can schedule a few visits to see your actual home being built. Walk-through your house while it's just a frame, and then see the design come together as your kitchen is installed. Grab a few photos so that, several years into enjoying your new home, you can look back at when it was being built especially for you.
Book your guided factory tour today.